Infrastructure
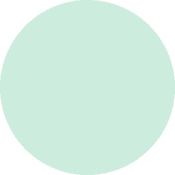

The Infrastructure
Big Bags International is a leading provider of comprehensive packaging solutions. Our state-of-the-art facility allows us to design, develop, and manufacture a wide range of fabric and flexible packaging products. With a global reach spanning over 20 countries and a strategic location near the Mangalore shipping port, we offer efficient delivery and exceptional customer service.


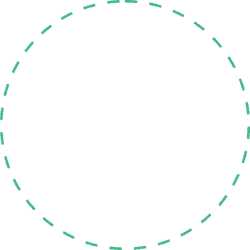
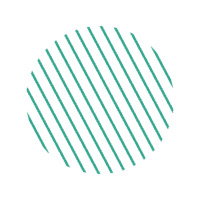

extrusion
We extrude 80,000 kgs of polymers per day

circular looms
We have circular 6-shuttle to 10-shuttle looms where we can produce 50 cm – 240 cm tubular fabric. We produce 250,000 meters of fabrics per day.

sulzer fabric looms
We produce Flat Fabric, Ventilated (Lock and Unlock), Leno, and Heavy Weight Fabrics, Type C & Type D ranging from 50cm to 400 cm flat fabric. We produce 15,000 meters per day.

lamination
We have a lamination plant that can produce lengths ranging from 1 meter to 4 meters, with thicknesses based on customer requirements. We laminate 90,000 meters per day.

lifting belt
We can produce widths ranging from 1.5 cm to 10 cm. We manufacture 250,000 meters of webbing per day and 20,000 meters of dustproof cord per day.

cutting
We have various types of fabric cutting like heat cutting, cold cutting, heat-seal cutting, and ultrasonic cutting.

4 – Colour Printing
We have a flexo-graphic printing facility where we can print up to 4 colours on all four sides of the FIBC. We can also provide BOPP printing on FIBCs as per customer requirements.

pe liner
We produce 35,000 meters of liners per day. 100,000 form-fit liners per month. We also produce baffle liners, square bottom, conical and special liners.

bag finishing
We produce 30,000 FIBCs per day. We have stitching patterns like Heracle plus safety, chain stitch, and lock stitch.

Net Baffle
We produce 5,000 meters of net baffle every day.
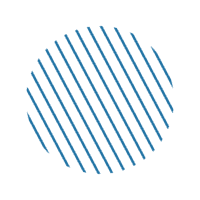
Clean Room Facility
We produce FIBCs from its state-of-the-art Clean Room facility to fulfil stringent customer requirements
Our facility is well integrated from fabric stage to packing with highly maintained hygienic conditions which adhere to global standards.
Our Clean Room is fully air conditioned and equipped with world-class equipment for ultrasonic cutting, air washing, metal detecting, etc.
Carefully selected personnel are highly trained in good hygiene and good manufacturing practices.
Big Bags has implemented HACCP (Hazard Analysis Critical Control Point) in its clean room facility to ensure optimum food safety.
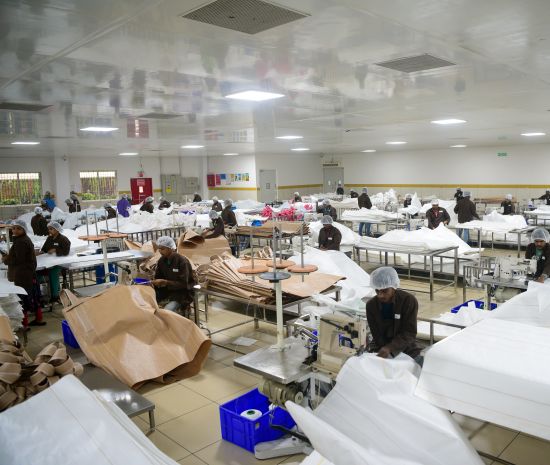
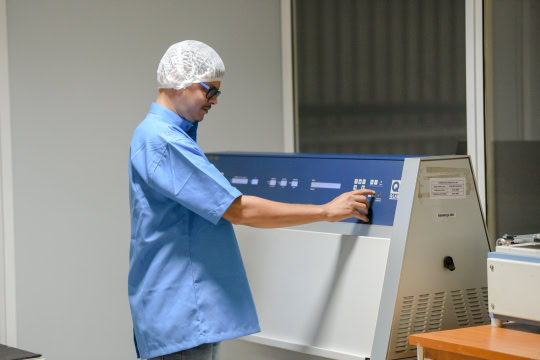
Testing Lab
We have equipment to check the breaking strength of tapes and also ultraviolet testing of tapes.
The other types of tests include Elongation Test, Load Test, Dart Impact Test, Co-efficient of friction testing (slip and anti-slip), Air Permeability test, Peel strength, conductivity testing, UN Testing as per Indian and international standards.